Bij Ventilair ontwikkelen we innovatieve ventilatiesystemen die bijdragen aan een comfortabele en energiezuinige woon-, werk- en leeromgeving. De eerste stap in het ontwikkelingsproces van elk nieuw product wordt gezet op onze afdeling Research and Development. Hier werken ze aan de (door)ontwikkeling van nieuwe en bestaande producten. Een afdeling, die vaak niet gezien wordt, maar wel erg belangrijk is voor het bedrijf. Daarom nemen we eens een kijkje achter de schermen bij de afdeling R&D.
Voor dit blog spraken we met Mike Marcuks, Engineer Productontwikkeling en samen met collega engineer A. van Roij, Technisch specialist Rick Gijzen en Manager Operations Rene Kiggen verantwoordelijk voor productontwikkeling van onze eigen Comair producten. Dit doen ze in nauw overleg met de productmanagers. Die geven de koers aan en bepalen prioriteiten in de te ontwikkelen producten. Hierdoor zijn de werkzaamheden ook erg afwisselend. “De ene week zijn we bezig met iets wat ruim van tevoren op de planning stond, de week daarop kan het iets zijn wat plotseling gedaan moet worden. Zoals bijvoorbeeld het identificeren van de oorzaak van een probleem dat een klant ondervindt”, vertelt Mike. We zijn in ieder geval vaak te vinden in ons (vernieuwde) testlab.
Testlab
In het Ventilair testlab worden mechanische eigenschappen van de producten getest. Denk hierbij aan het bepalen van minimale/maximale trekkracht en drukkracht welke onze producten kunnen weerstaan. Ook kunnen vervormingen aan de producten worden gemeten onder belasting. Daarnaast testen we ook onderdelen en systemen op luchtdichtheid en de drukval die de producten creëren in een compleet systeem. Dit testlab is dus best belangrijk voor ons.
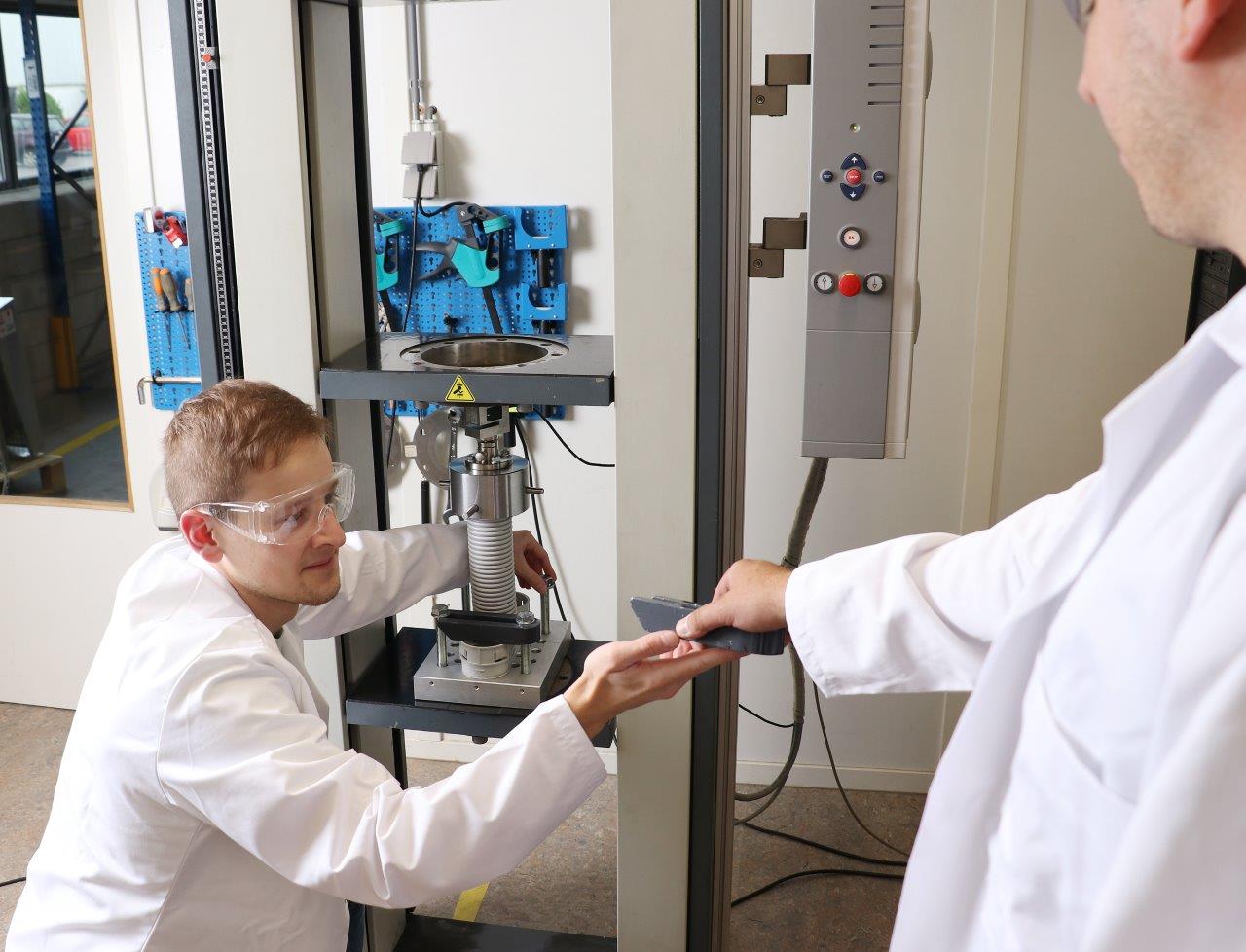
Onlangs heeft het testlab een grote update gekregen. Er zijn nieuwe testopstellingen gemaakt van onze ventilatiesystemen en ook zijn er op het gebied van testapparatuur verbeterstappen gemaakt. Zo is er een nieuwe materiaaltestmachine (trekbank) geplaatst waarmee we bijvoorbeeld de kracht kunnen meten die nodig is om onze flexibele slang in het klikdeel te klikken. Tevens is er een nieuwe oven en een blastchiller bij gekomen. Hiermee kunnen we testen conditioneren op hogere of lagere temperaturen. Daarmee zorgen we ervoor dat onze producten zich onder alle omstandigheden blijven gedragen zoals het zou moeten in de praktijk.
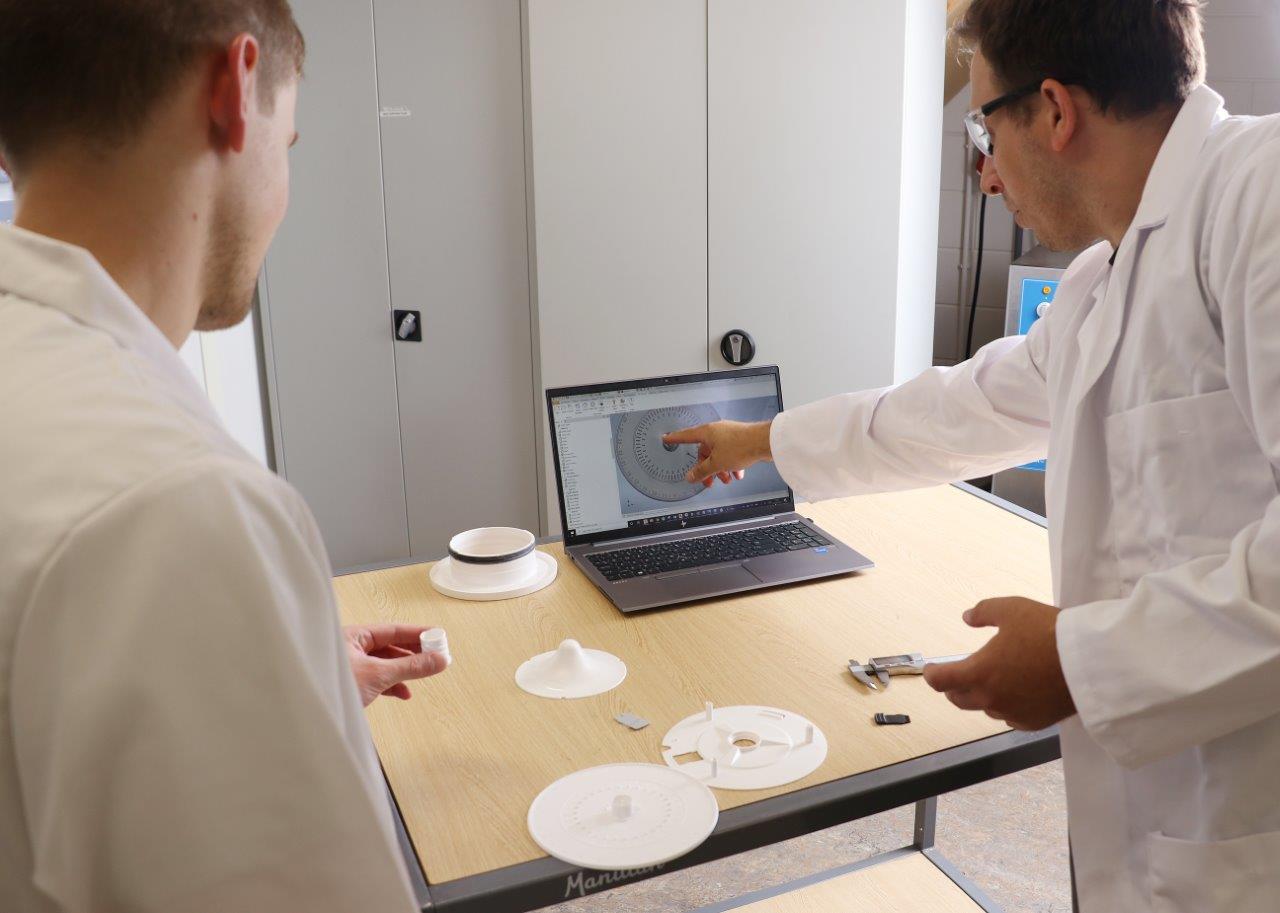
Versnelling in het ontwerpproces
“We kunnen met de nieuwe apparatuur nauwkeuriger meten. Zelfs de kleinste verschillen in mechanisch gedrag van prototypes en producten zijn nu meetbaar”, vertelt Mike. Dit versnelt met name het ontwerpproces. We kunnen sneller voor een bepaald design en/of materiaal kiezen. Met de blastchiller en oven hebben we bijvoorbeeld goed uit kunnen zoeken wat de beste materiaalkeuze zou zijn voor onze klikdelen van het Comair FLX luchtverdeelsysteem. Voorheen moesten we dit uitbesteden. Dat kost vaak toch meer tijd en geld.
Op de vraag of we nu alles in eigen huis kunnen testen is Mike duidelijk: “We kunnen nu vrij veel zelf testen en we werken continu aan een roadmap voor toekomstige apparatuur. Echter, blijven er altijd zaken die je beter door specialisten kan laten doen. Denk dan bijvoorbeeld aan onderzoek naar de exacte samenstelling van materialen, geluidstesten, simulaties van luchtstromingen in onderdelen, of simulaties van het spuitgietproces. Maar ook daarvoor hebben we onze contacten”, aldus Mike.
Met de huidige apparatuur is het ook mogelijk om normen aan te houden en dus resultaten te verkrijgen die gebruikt kunnen worden in officiële rapporten en certificaten. Echter, vinden we het zelf ook fijn om deze op te laten stellen door een derde partij ter controle.
Duurzaamheid
Ook binnen de R&D afdeling krijgt het thema duurzaamheid een steeds belangrijkere rol. We focussen steeds meer op de recyclebaarheid van onze producten. Zo moeten materialen van elkaar gescheiden kunnen worden bijvoorbeeld. Hiervoor lezen we documentaties, volgen we kennissessies en kijken we in hoeverre nieuwe en bestaande producten in de toekomst geproduceerd kunnen worden op een duurzamere manier.
Maar duurzaamheid zorgt ook nog voor obstakels. Zo is de keuze voor gerecycled materiaal er eentje van compromissen. Er zijn verschillende vormen van gerecycled kunststof. Er is materiaal genoeg beschikbaar in de markt, echter omdat we met lucht in onze systemen werken is de geur van onze producten belangrijk. Het overgrote deel van gerecycled plastic heeft een minder fijne geur (en kleur). Je denkt er misschien niet meteen aan, maar dat zijn zaken waar we rekening mee moeten houden als we een product ontwikkelen dat van gerecycled materiaal gemaakt gaat worden.

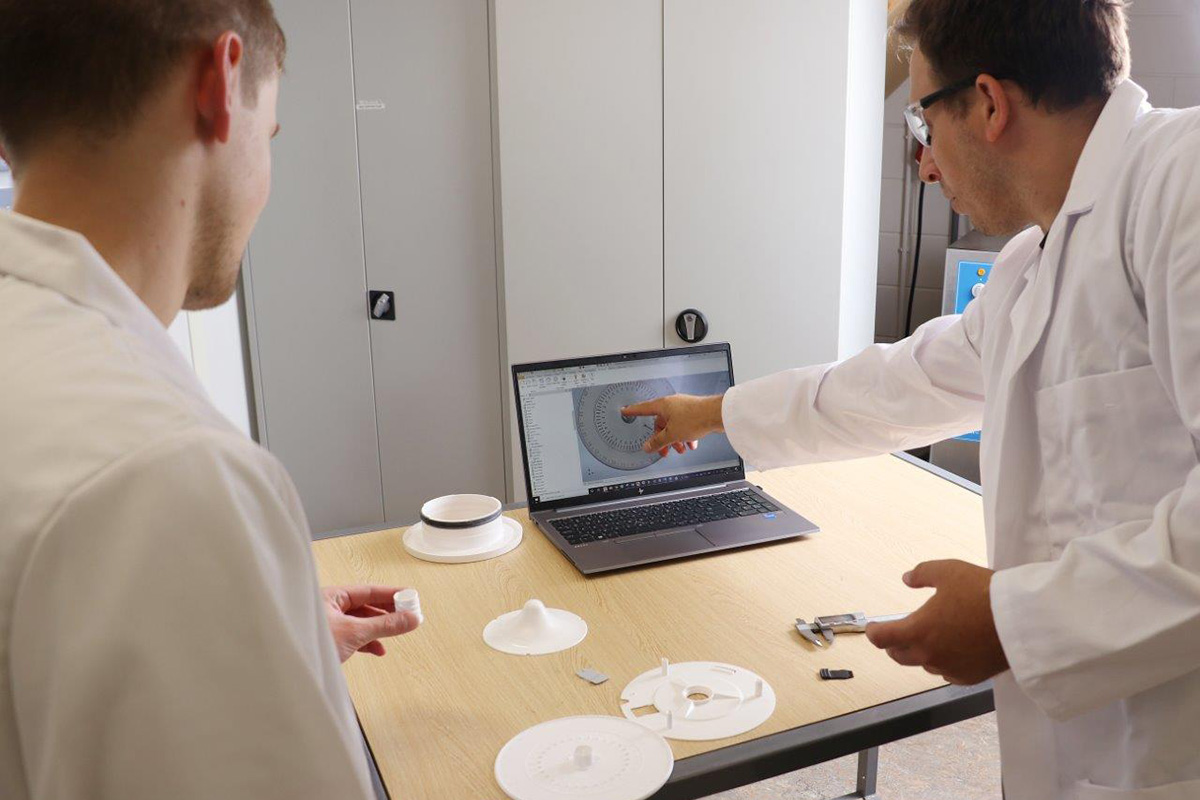
Toekomst
Voor Mike en zijn collega's is het belangrijk om naar de toekomst toe de ogen en oren open te houden. Zo zijn we momenteel veel bezig om onze producten gereed te maken voor de industriële woningbouw. Want er wordt steeds meer prefab gebouwd en hiervoor moeten onze producten ook doorontwikkeld worden. En dat is niet binnen een paar dagen gedaan.
We blijven op de hoogte van alle product- en marktontwikkelingen via vaktijdschriften, kennissessies en workshops. Ook bezoeken we regelmatig beurzen en volgen we cursussen. Daarnaast zetten we in op samenwerkingen met universiteiten en kennisorganisaties. Belangrijk is om ons te blijven richten op materialen en productieprocessen die aan de duurzaamheid van onze producten bijdragen. Zo blijven we ook ons zelf ontwikkelen.